1、金屬基復合材料的磨削
顆粒增強金屬基復合材料磨削加工是借助磨具的切削作用,除去工件表面的多余層,使工件表面質(zhì)量達到預定要求的加工方法。常見的顆粒增強金屬基復合材料磨削加工形式有外圓磨削、內(nèi)圓磨削、成形面磨削等。金屬基復合材料的磨削特性受增強相類型和所用砂輪類型的影響,增強顆粒的存在改善了材料的磨削性能,軟的基體金屬堵塞砂輪是砂輪失效的主要原因,磨削加工中的主要問題是砂輪堵塞及磨削區(qū)的有效冷卻。在實驗條件下,
平面磨床磨削顆粒增強金屬基復合材料時,碳化硅砂輪在磨削力、表面粗糙度等方面優(yōu)于CBN和金剛石磨料砂輪。使用陶瓷基SiC砂輪和樹脂結(jié)合劑金剛石砂輪對氧化鋁顆粒增強鋁基復合材料進行的磨削表明,SiC砂輪可以用于粗磨,粗磨時工件的磨削表面上有基體金屬的涂敷現(xiàn)象,降低了表面粗糙度。
金剛石砂輪適合于精磨,精磨時基體材料沒有明顯的涂敷現(xiàn)象。使用細粒度金剛石砂輪在磨削深度為1um的情況下實現(xiàn)了材料的延性磨削,表面及亞表面上沒有裂紋和缺陷產(chǎn)生,實現(xiàn)了增強相的延性去除。磨削是顆粒增強金屬基復合材料加工中很有前途的一種加工方法,能夠?qū)崿F(xiàn)無損傷表面的加工。
采用電鍍金剛石砂輪平面磨削顆粒增強鋁基復合材料,工件材料為SiC顆粒增強2024A1,其主要性能參數(shù)如表1所示。平面加工中采用普通的平頭圓柱砂輪,金剛石粒度為120目,砂輪直徑為20.6mm。
表 工件材料參數(shù)
質(zhì)量分數(shù) | 屈服應(yīng)力 | 顆粒尺寸 | 彈性模量 | 伸長率 | 密度 |
50 | 271.3 | 10 | 199.8 | 0.431 | 2.90 |
主軸轉(zhuǎn)速取6000r/min,進給速度為300mm/min,取磨削深度從0.001mm至0.05mm進行磨削試驗。加工表面形貌如圖1所示。
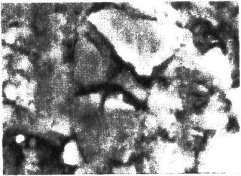
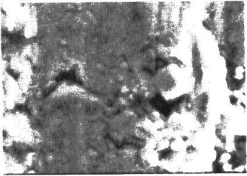
(a)削落瞪坑 (b)顆粒破碎 (c)界面脫落
圖1 平面磨削加工表面形貌
加工表面質(zhì)量具有如F特征:
?、偌庸け砻嫔嫌袖X基體的塑性劃痕,并且有鋁基體被熨壓現(xiàn)象;
②加工表面有材料剖落形成的凹坑、增強顆粒脫落和斷裂等缺陷;
?、垲w粒與基體結(jié)合的界面在已加工表面形成過程中發(fā)生破壞。由于顆粒移動或被壓入加工表面,在顆粒周圍形成孔洞。加工表面的形貌特點與材料本身特性和去除機理有關(guān),在外載荷作用下增強顆粒承受更大的應(yīng)力及增強顆粒本身的缺陷,使得增強顆粒在加工過程中產(chǎn)生破碎和脫落;裂紋的產(chǎn)生和擴展在加工表面形成過程中起到重要作用,在增強顆粒富集區(qū)和顆粒的尖角處應(yīng)力集中更嚴重,在加工過程中容易產(chǎn)生裂紋并擴展,造成材料剖落形成非切出表面和界面脫黏;另外,在金剛石磨粒作用下增強顆粒會發(fā)生破碎、脫落、滑動等行為。
保持主軸轉(zhuǎn)速為6000r/rain、進給速度為300mm/min不變,測量了在不同磨削深度下已加工表面的粗糙度值,如圖11—8所示??梢钥吹?,在實驗所采用的加工參數(shù)下,表面粗糙度Ra在0.85~0.82tzm之間。磨削深度在0.001~0.005mm范廚內(nèi)時表面粗糙度的變化不大,而當磨削深度大于0.005ram之后表面粗糙度有較大的增加。
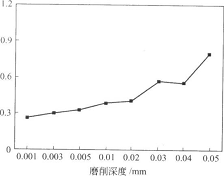
圖2磨削深度對表面粗糙度影響
2、碳纖維增韌碳化硅陶瓷基復合材料(c/SiC)的磨削
碳纖維增韌碳化硅陶瓷基復合材料(C/SiC),具有密度低、抗氧化性好、耐腐蝕、摩擦磨損性能良好以及耐高溫等優(yōu)點,能夠滿足防熱——結(jié)構(gòu)一體化設(shè)計的需要,成為空天飛行器等關(guān)鍵熱結(jié)構(gòu)的重要候選材料,并已成功應(yīng)用于航空航天領(lǐng)域。
工件材料為碳纖維體積分數(shù)約為45%、密度約為2.0g/cm3的2D-C/SiC復合材料。砂輪為樹脂結(jié)合劑金剛石砂輪,砂輪粒度120,砂輪直徑300mm,砂輪寬度20mm。金剛石砂輪修整采用普通SiC砂輪與金剛石砂輪對磨的方法實現(xiàn)。磨削方式為順磨,冷卻液為普通水基冷卻液。磨削參數(shù):進給速度-20~50mm/s,磨削速度-60~90m/。,切削深度-0.1~0.3mm。為了觀察到工件的亞表面損傷,首先對垂直于磨削方向的面依次采用800#、1200#、1500#及2000#的金剛石研磨粉進行研磨至鏡面,材料去除厚度大于200nm,然后采用超聲波清洗器對試樣進行清洗,再用烘箱烘干試樣,最后通過掃描電鏡(SEM)對磨削表面和亞表面進行觀察。磨削前、后的表面形貌見圖3,2D-C/SiC的表面形貌掃描電鏡照片見圖,通過分析磨削結(jié)果發(fā)現(xiàn):
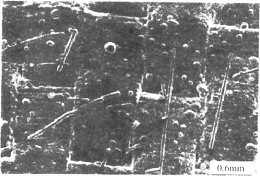
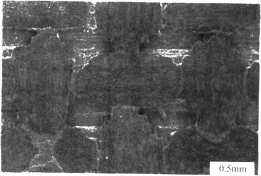
(a)磨削前 b)磨削后
圖3 2D-C/SiC磨削前、后表面形貌的比較
?、?D-C/SiC復合材料的高速深磨材料去除機制與其自身的微觀結(jié)構(gòu)相關(guān),既不同子塑性材料,也不同于普通脆性材料,而是以脆性斷裂去除為主。
?、谀ハ鲿?D-C/SiC復合材料表面部分被SiC基體覆蓋的原始孔隙重新顯現(xiàn)出來,通過再次氣相沉積SiC基體能使其致密化和均質(zhì)化程度得到提高,從而達到改善材料綜合力學性能的目的。
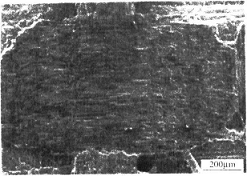
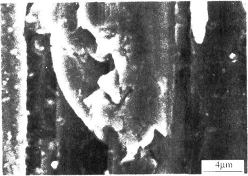
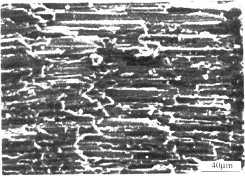
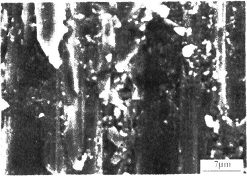
圖4 2D-C/SiC的表面形貌掃描電鏡照片
③由于SiC陶瓷基體和碳纖維兩者導熱性和熱膨脹性的差異及2D—c/sic復合材料自身存在的孔隙缺陷,磨削加工后,產(chǎn)生了特殊的已加工表面結(jié)構(gòu)。2D-C/SiC材料已加工表面并非全部由磨粒直接切出,因此,難以準確評價其已加工表面質(zhì)量。
?、軆H考慮磨削2D-C/SiC復合材料表面摩擦層的情況下,
磨床磨削力隨磨削深度和工件速度的增加而增加,隨砂輪線速度的增加而減小。磨削深度對磨削力的影響最大,砂輪線速度和工件速度對磨削力的影響大致相同,但作用相反。增加工件速度,降低砂輪速度有利于減小磨削力比;增加磨削深度對磨削力比的影響不顯著。