(1)硬質(zhì)合金的晶粒度對磨酎性能的髟響
硬質(zhì)合金是由高硬度、難熔鈞金屬碳化物(如WC、TiC、TaC,NbC等)加金屬黏結劑(如鈷、鎳等)經(jīng)粉末冶金工藝制成,是目前世界上強度最高的合金,具有硬度高(89~93Hm)、強度高、熱硬性好等特點。因此,被廣泛應用予勘探鉆頭、模具、工具的制造。隨著切削加工技術向高速、高精方向的不斷發(fā)展,要求硬質(zhì)合金工具的硬度、耐磨性、磨床加工精度和刃口質(zhì)量越來越高。硬質(zhì)合金的晶粒度也由最初的粗晶(晶粒度6~25um)、中晶(1.3~2.5tum),逐步向細晶(0.8~1.3um)、超細晶粒(0.2~0.5um)、納米晶粒(≤0.2um)方向發(fā)展。
目前,粗晶硬質(zhì)合金廣泛應用在地礦工具、沖壓模具、石油鉆采、生產(chǎn)人造金剛石用大頂錘、噴氣發(fā)動機部件等領域;細晶及超細晶粒硬質(zhì)合金具有硬質(zhì)合金的高硬度和高強度的特點,主要用于整體硬質(zhì)合金刀具、可轉(zhuǎn)位刀片及加工印刷電路板的微型鉆頭等工具的制造。
隨著硬質(zhì)合金中WC晶粒的細化,合金的硬度、強度等力學性能增加,斷裂韌性等性能下降,耐磨性等磨削加工性能也隨之發(fā)生了一定的變化。
采用三種不同粒度金剛石樹脂結合劑砂輪,分別針對粗、細、超細三種不同晶粒度的硬質(zhì)合金,在一定的磨削條件下進行磨削試驗。通過對磨削過程中平面磨床主軸功率、砂輪和工件損耗、加工表露粗糙度的測量,分析硬質(zhì)合金中WC的晶粒度變化對磨削力、磨削比、表面粗糙度等磨削性能和效果的影響。
磨削試驗條件為:萬能工具磨床,往復式
平面磨床磨削方式,砂輪轉(zhuǎn)速ns=3200r/min,磨削速度Vc=25m/s,工件速度uw=15m/min,冷卻液LTY-1(水液比為20/14),工件選用不嗣粒度的K系列硬質(zhì)合金,含Co量均為10%。其微觀組織如圖1所示。
通過試驗可知,在
平面磨床各磨削參數(shù)相同的情況下,磨削粗晶硬質(zhì)合金所消耗的磨削力、磨削能大于細晶和超細晶粒硬質(zhì)合金,且平面磨床磨削力隨晶粒尺寸的增大而增加;同一砂輪對粗、細、超細硬質(zhì)合金的磨削比隨晶粒粒徑的增加而增大,說明該類硬潢合金的耐磨性隨晶粒粒徑的增加而降低;該類硬質(zhì)合金在相同磨削條件下精磨加工后的表面粗糙度隨晶粒尺寸增加而變差。
(2)平面磨床磨削參數(shù)對超細硬質(zhì)合金磨削表面粗糙度的影響
使用金剛石砂輪的磨削加工是生產(chǎn)硬質(zhì)合金刀具的主要方法,磨削表面粗糙度對硬質(zhì)合金刀具的切削性能和使用壽命有重要的影響,而磨削參數(shù)是影響硬質(zhì)合金表面粗糙度的主要因素。
在M71,20型平面磨床上對WC-Co硬質(zhì)合金試樣進行磨酣試驗,試件為采用HIP技術燒結的超細晶粒硬質(zhì)合金。磨削工藝參數(shù)見表1。
超細晶 細晶 粗晶
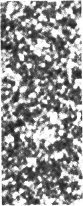
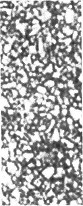
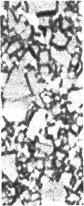
圖1 不同晶粒度硬質(zhì)合金的微觀組織圖
表 磨削工藝參數(shù)
砂輪轉(zhuǎn)速 ux/m·S-1 | 工作臺速度 uw/m·min-1 | 砂輪粒度 | 單次切深 ap/um |
20 | 30 | 150# | 5,10.15,20,25 |
280# | 10 |
W20 | 10 |
在相同切深(ap=10um)條件下,試樣磨削表面粗糙度隨砂輪粒度的變化情況見圖2。
由圖可見,同一切深下,試樣磨削表面粗糙度隨砂輪粒度的增大而增大。但砂輪粒度對表面粗糙度的影響程度有所不同,與150#砂輪比,使用280#砂輪磨削,試樣磨削表面粗糙度變化幅度較小,而使用W20砂輪磨削,表面粗糙度變化幅度較大。圖3顯示了使用同一粒度砂輪(150#)磨削,試樣磨削表面粗糙度隨切深口,變化的規(guī)律。由圖可見,當ap≤15um時,試樣磨削表面的粗糙度隨ap的增加近似地呈線性增大。但當ap>15um后,隨切深的增大,
磨床磨削表面粗糙度值逐漸減小,這一點與傳統(tǒng)結構硬質(zhì)合金的磨削試驗結果有所不同。
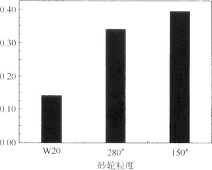
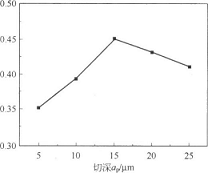
圖2 砂輪粒度對表面粗糙度的影響 圖3切深對表面粗糙度的影響